CONSTRUCTION
STORY OF
SCRATCHBUILT
STREET ROD
|
 |
Building Period: 30 March 1999 - 30 June 1999
PART
3
REAR SUSPENSION
The rear suspension is assigned to be
a leaf spring type. The reason was simply to make the model of a
different
kind of suspension. The leaves are cut from 0.2 mm brass sheet and
given
an approximate curvature by hand.
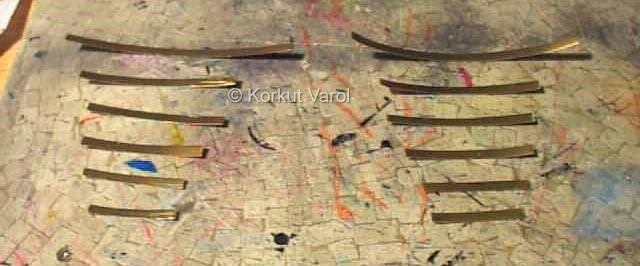
The leaves were pre-soldered (both
sides)
at their middle and held together firmly with a clamp. The center part
was heated with soldering iron to melt and join the leaves. However,
the
power of the soldering iron proved to be small for the job. There was a
lot of metal around to absorb heat faster than the iron could supply.
So
a small propane torch was used to melt the metal and hold the leaves
together.
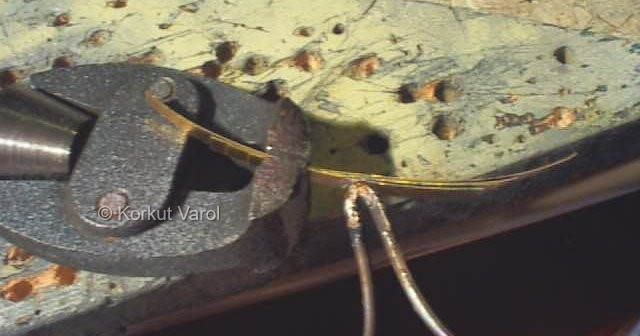
Now the leaf spring pair was ready
for
further treatment.
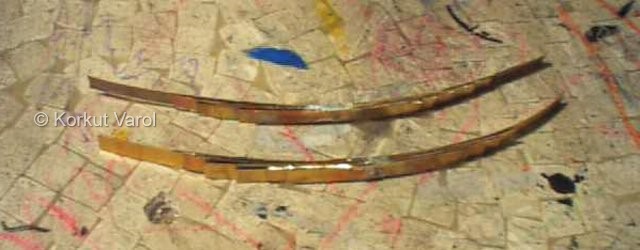
The rear leaf spring brackets are
made
from 1 mm thick brass sheet at the outside, and 0.2mm thick brass sheet
at the inside. The pin holes are being drilled on the outer element in
the picture at right.
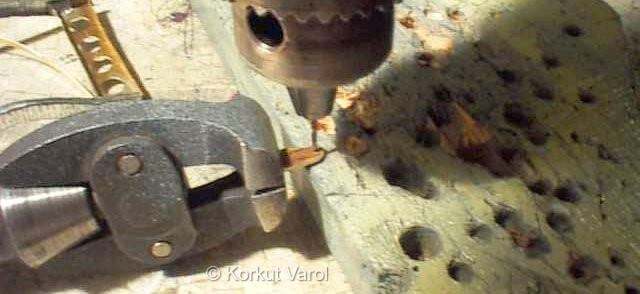
The inner and outer elements of
the bracket are being soldered. The unit resembles the letter "h" and
the
side and bottom surfaces of the chassis will mate with that "h" profile.
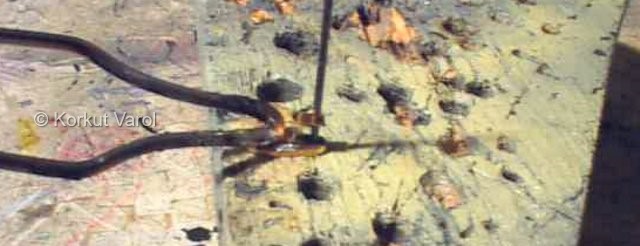
Now the bolting holes are drilled
with
1mm. drill and pins located in the holes to resemble the bolts. They
are
fastened by CA glue and after drying, the protruding stems of the pins
are cut off flush with the surface.
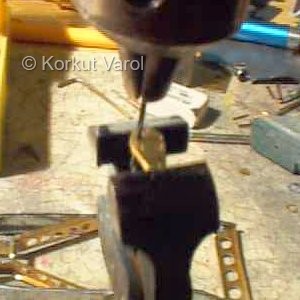
The spring brackets are fastened to
the
chassis with 5-minute epoxy. Trying to solder them would melt away the
solder that grouped the "h" shape of the brackets. The rearmost
brackets
were too small to handle for drilling, so the imitations for bolt heads
were made by applying tiny droplets of CA glue.
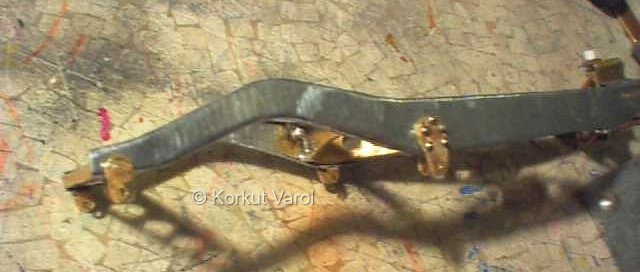
The front eyes of the leaf springs
are
made by wrapping the end of the first leaf over a pin and defining the
roundness of the eye by squeezing with pincers. The excess part left after forming
the
eye is cut off with the cutter tip of a Dremel moto-tool.
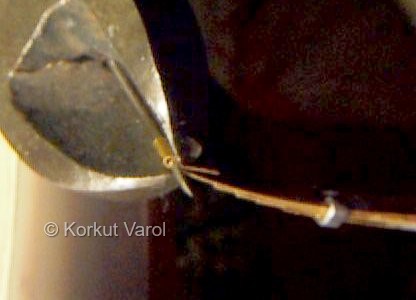
The other end
of the spring is of sliding type, and its profile is formed by hand.
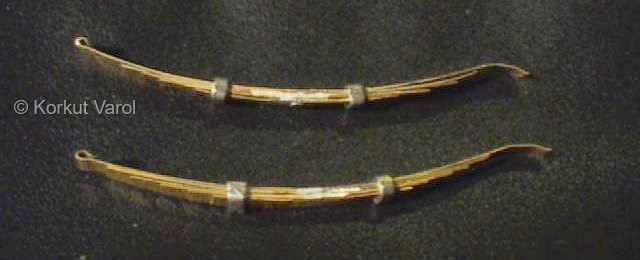
A test mounting of the springs to see
if things are going OK.
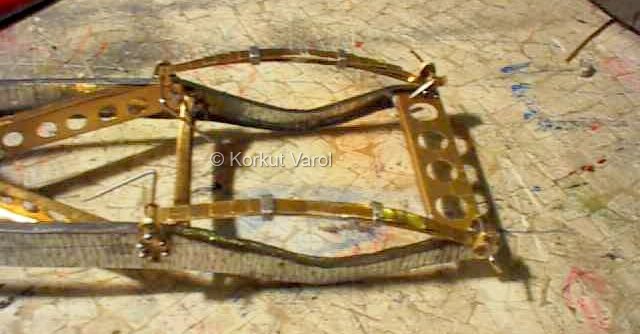
The height of the spacer block
between
the spring and the axle is calculated and suitable blocks from eraser
are
cut with X-acto knife. The rear axle is turned from a steel rod ready
in
hand and channels were machined at both ends to house two snap rings
that
will aid in defining a perpendicular plane for the mounting of the rear
hub parts. The blocks are secured on the axle by CA glue.
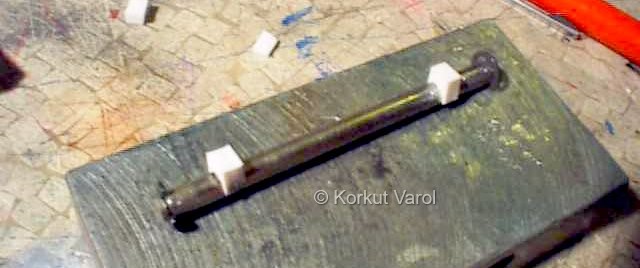
The differential is home-cast resin
by
using the differential housing parts of a '67 Mustang still in its box.
The front and rear halves are brought together on the axle and the
small
gap left between them will be filled with putty.
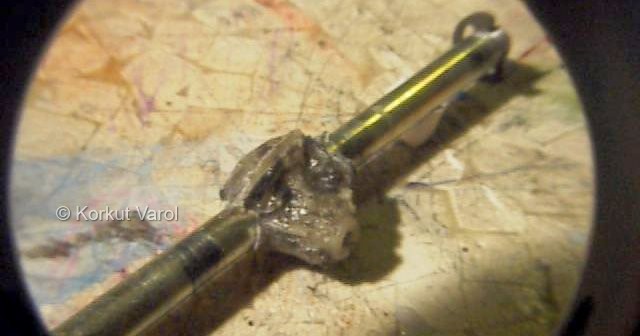
Now the axle is glued on to the
springs
with 5-minute epoxy. Care was taken to maintain correct wheelbase and
intermediate
measures were made to make sure that the axle did not slip while curing.
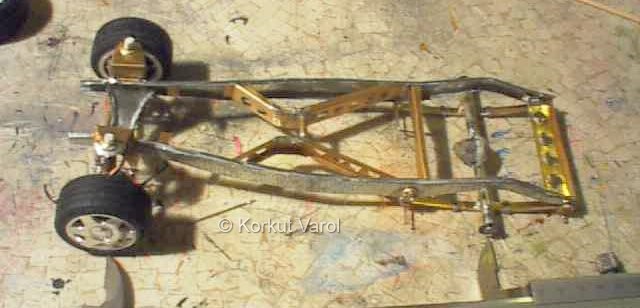
The U-bolts were made from pins and
the
tightening plates from 1 mm lead sheet. Holes were drilled on the
plates
so that the U-pins (Sorry....U-bolts) would go through them.
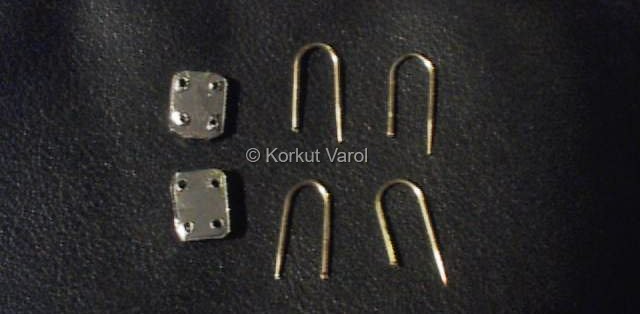
The assembly is held together by
5-minute
epoxy glue.
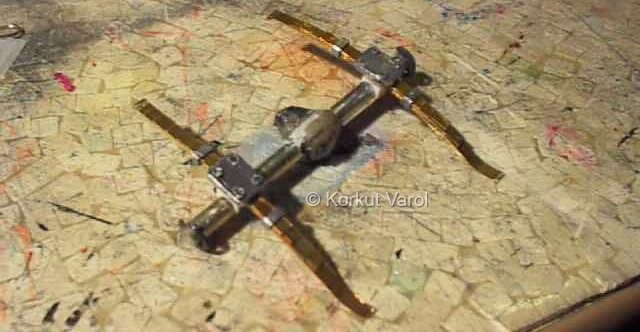
A close-up of the U-bolt region.
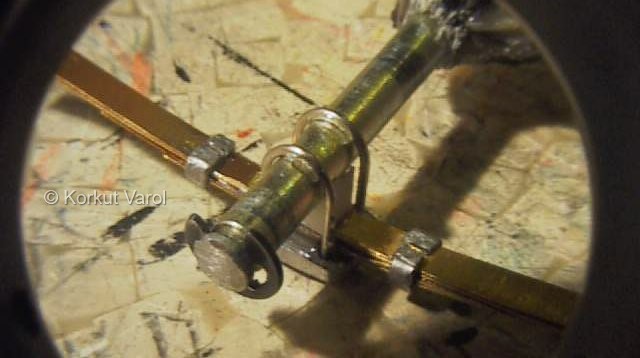
........................
.....................